Recent Posts
-
2024.04.27
ミラノサローネ研修に行ってきました
-
2024.04.26
CERVOⅡ AD-961・971
-
2024.04.16
ホテルで使われている製品
-
2024.04.05
大阪・心斎橋ショールームへお越しください
-
2024.03.29
カリフォルニアスタイルの先駆者
-
2024.03.27
出荷前の製品画像確認を行っています
-
2024.03.26
MD-1301C-OP
-
2024.03.26
MEDUSA AD-981
-
2024.03.26
インテリアコーディネートの参考に
-
2024.03.25
季節に合わせてショールームも春らしく
Back Number
2024年
2023年
2022年
2021年
2020年
2019年
2018年
2017年
2016年
2015年
2014年
2013年
2012年
2023.12.26 DESIGN
家具を作ることの難しさ
AD CORE DEVISE DESIGN BLOG Vol.140
2023年のスタートは新型コロナ感染がはじまって3年が経過し、ようやく収束の目処が見えてきたところでした。昨年末も暖冬から一転、記録的な積雪でしたから、ちょうど今の状況と同じような天候だったんですね。あっという間の1年でしたが、さまざまな出来事がありました。皆さんにとって今年はどんな一年だったでしょうか。私にとっては、規格製品を異なる工場で作ることの難しさを実感した一年でとなりました。
エーディコア・ディバイズでは、製品化した家具を製品に適した工場へ生産を依頼します。当社のクオリティーを理解いただき品質をキープ出来る工場へお願いしています。生産をお願いする私たちと、家具を作り上げる工場とでお互いに信頼し合える関係が築けるところになるのでたくさんあるわけではありません。椅子・脚モノを中心にお願いしている山形の工場と、ソファ・テーブルは九州大分県の日田市にある工場に生産をお願いしています。ところが今年の7月、山形の工場で火災が発生してしまい生産が出来なくなってしまいました。ブランド発足から長い間生産していただいてた工場が、突然モノが作れなくなってしまった緊急事態です。火災の被害は思いのほか深刻で復旧の目処が立たない状況で、一刻も早く当社の家具の生産移行をする必要に迫られました。生産の優先順位とアイテムの精査、図面の準備から仕様指示書の確認をし生産をお願いできそうな工場を当たりました。当社でデザイン、開発した製品、家具として生産が流れているモノです。仕様も注意点もわかっているのですから、工場の設備が整っていれば基本的には生産移行が出来ると考えていました。しかし大変だとは覚悟していましたが生産移行は想像以上に困難な作業でした。
現在お願いしている工場以外で、生産をお願いできそうな可能性のある工場をあたりました。しかし、国内で家具の生産工場がどんどん減少していく中、生産キャパに余裕がある工場はほとんどありません。「生産が落ち着いたら」「状況が整ったら」といった回答もありましたが、受けていただける工場もありました。「自社のレベルアップのためにも是非」「生産前提で前向きに進めます」など、快諾いただいた工場にはすぐに訪問して打ち合わせを行いました。できるだけ移行がスムーズに進むよう、ブランドのコンセプトから生産の流れ、製品の資料をお渡しして準備を進めたのですが・・・全く思うようには進みませんでした。製品化されているとは言っても、他の工場で新しく作るとなると一から新製品を開発するの同じくらい労力を要します。製作仕様書があればそのまま作れば手間暇省けるだろうと考えてしまいますが、設備や各工場の「やり方」があるので、逆に仕様書に縛られて進まなかったりコストが余計かかってしまう、ということは後になってから気がつきました。当社のブランドコンセプトでもある「どこにでもあるようでどこにもない家具」普通に見える家具でも、仕口や構造が難しいためなのか「当社では対応出来かねます」と、途中でお断りされるケースもありました。私たちには当然のクオリティーでも他の工場からすると「かなり難しい」という声もたくさんありました。資材入手や突板の張り分け加工なども問題で、今までは当たり前に思っていた様々なことが難しくなってきているのだと思います。
暑さ厳しい真夏から何度も工場へお伺いし、皆様からご協力いただきながら19アイテムの生産移行を開始することができました。生産ラインが軌道に乗るまではまだ確認が必要ですが、他の製品も引き続き作業を進めてまいります。今年はいろんな工場の方にお話をお聞きする機会があり、モノ作りの現場で感じている難しさに色々と思うこともありました。来年はそんな取り組みにも向き合っていきたいと思います。(開発 武田伸郎)
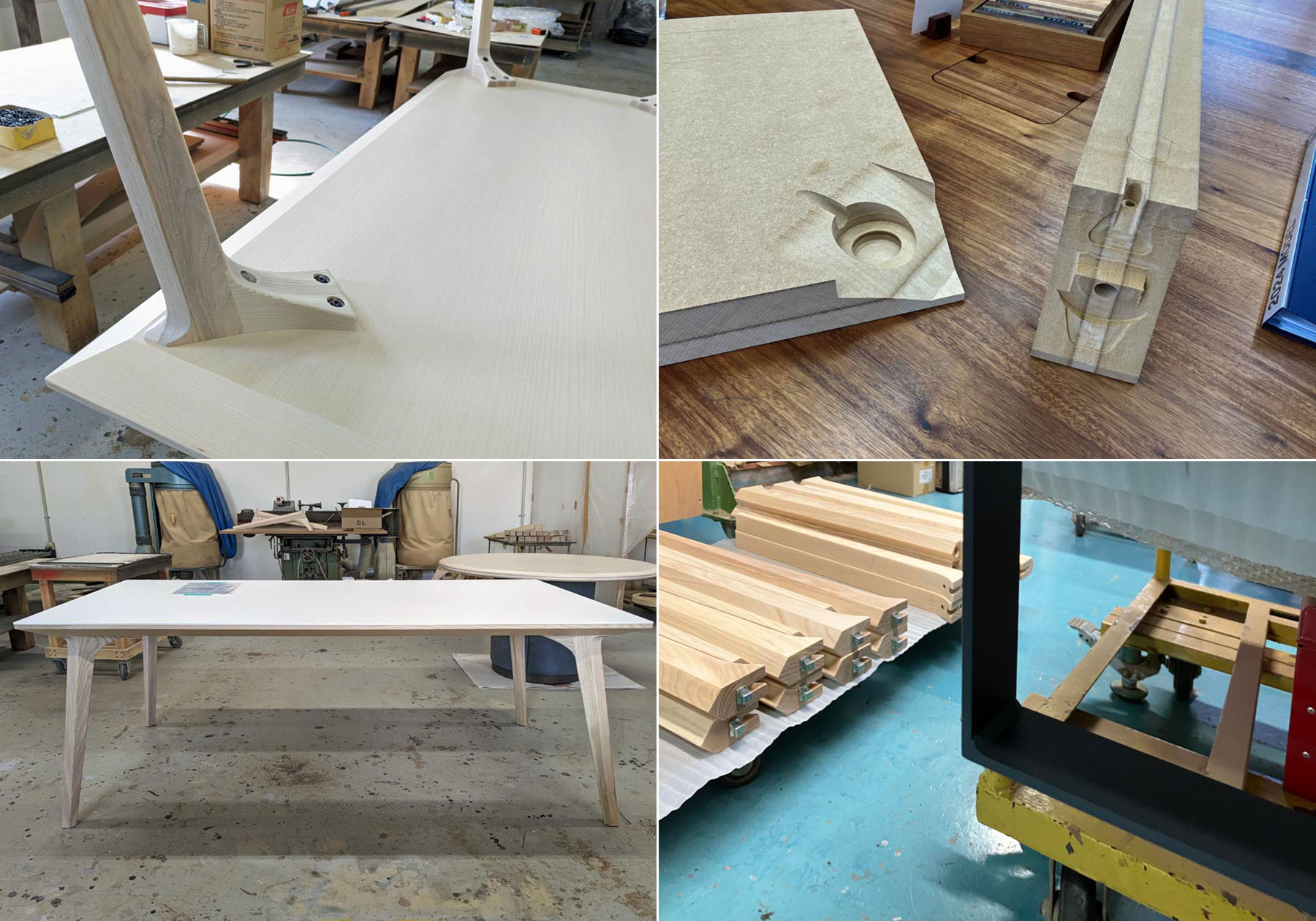
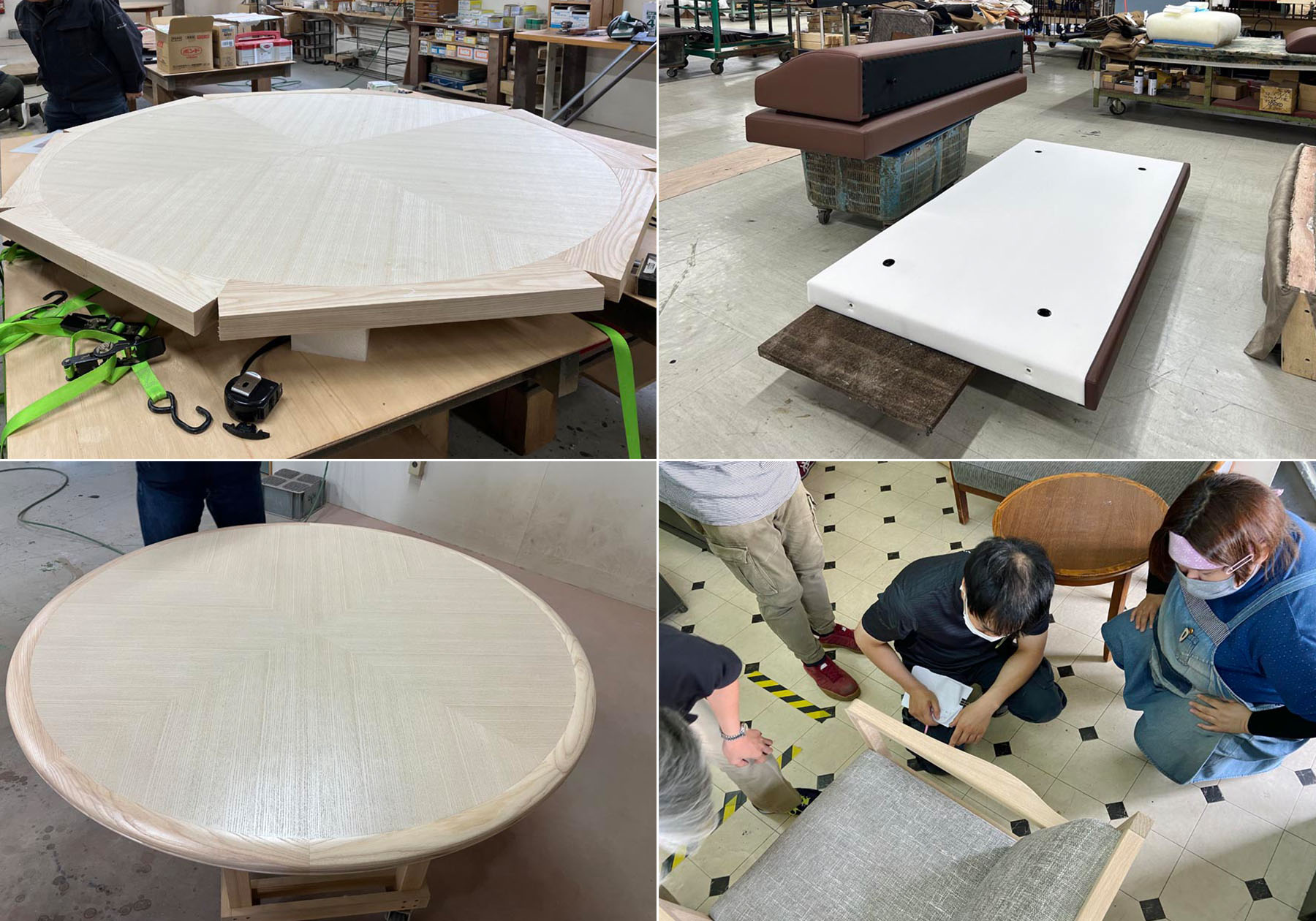